What are Brushless DC Motors
Brushless DC motors (BLDC) are popular in various applications and have good controllability and high efficiency. An electric motor having a stator and rotor that commutates by electrically synchronizing the currents are known as a brushless motor. A magnetic field is created as current passes through the three stages of the winding and interacts with the permanent magnets on the rotor to cause rotation around the center axis.
Advantages of BLDC Motors
Compared to other motor types, the brushless DC motor provides advantages for power conservation.
Efficiency
Efficiency is a significant benefit, as these motors can continually control at maximum rotational force also known as torque. As opposed to this, only a few places throughout the rotation of a brushed motor will produce its maximum torque. A brushed motor would require large magnets to provide the same torque as a brushless type. Because of this, even tiny brushless DC motors may provide significant power.
Controllability
Controllability is the second significant benefit, which is related to the first. You can use feedback systems to control BLDC motors to provide the desired torque and rotation speed. Precision control thus lowers energy consumption, generates less heat, and extends battery life in the case of battery-powered motors.
Durability and less noise pollution
Another advantage of a brushless motor is durability and less noise pollution. Due to the absence of brushes, brushless DC motors also provide good durability and low electric noise production. Brushed motors emit sparks wherever there is contact, which causes the brushes and commutator to wear out over time.
Strong sparks that frequently happen where the brushes cross commutator gaps are the cause of electrical noise in particular. It is the reason why BLDC motors are frequently regarded as the best option in applications where it is crucial to prevent electrical noise.
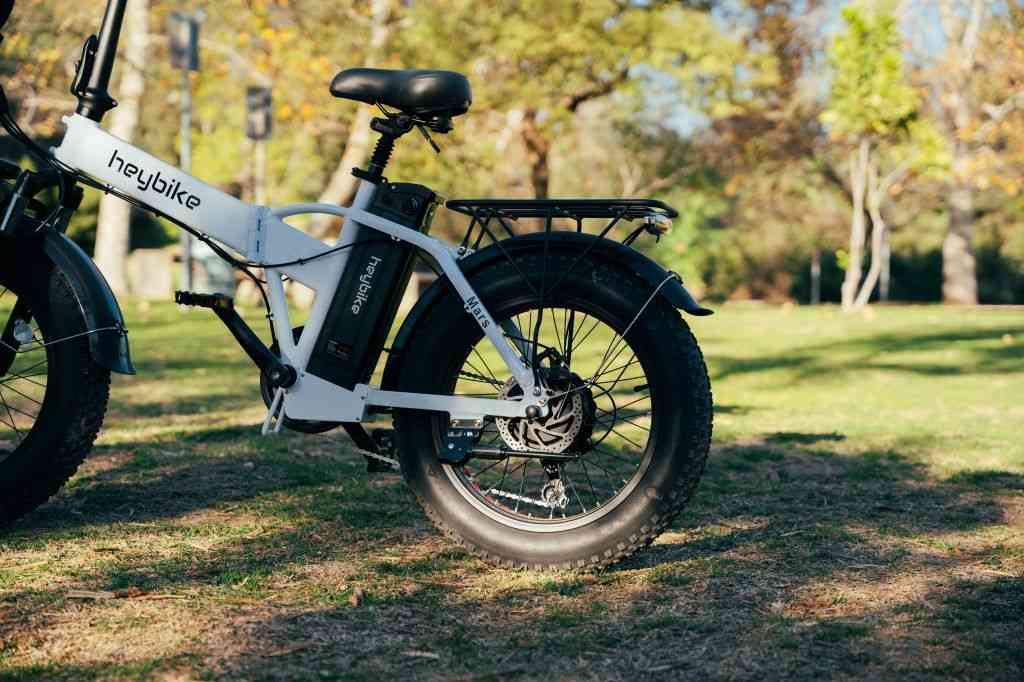
Drones can also benefit from BLDC motors. They are particularly well suited for multirotor drones, where the drone is controlled by accurately adjusting the rotational speed of each rotor because of their ability to give precision control.
Brushed Vs. Brushless Motor on Different Aspects
Cost
Because brushless motors require more complicated circuitry, a brushless drive is more expensive overall than a brush motor. Brushless motors are more difficult to create than brushed motors because they lack brushes and commutators, while brushed motor technology is more established and less expensive. The use of brushless motors is evolving, especially in high-volume applications like automotive motors. Additionally, the ongoing decline in the cost of electronics like microcontrollers has increased the demand for brushless motors.
Efficiency
Friction is also created because the brush must be in touch with the commutator to transmit a charge. The reason friction raises the temperature while reducing the speed that can be reached. It is similar to riding your bike with the brakes barely engaged. You will move more slowly even with the same amount of leg exertion. On the other hand, it will require more effort from your legs to keep up the tempo. The frictional heat will also cause your rims to warm up. Thus, brushless motors operate more coolly than brushed motors. They become more efficient as a result, converting more electricity into power.
Torque
Riders misunderstood the relationship between torque and brushless motors. The amount of torque is not indicated by the brushless or brushed motor design itself. But eventually, manufacturers understood something crucial. When necessary, the electronics in brushless motors can provide motors extra power. Modern brushless motors can detect when they start to slow down under load because they use sophisticated electronic controllers.
Lifetime
The mechanical wear and tear of the brushes and commutators in brushed motors have already been addressed as one disadvantage. Carbon brushes are designed to be replaced regularly as part of a maintenance routine in many bike motors. In addition, the brushes gradually tear the soft copper of the commutator until the bike motor is rendered useless. Because their contacts are not moving, brushless motors do not suffer from this wear.
Speed and Acceleration
The mass of the rotor can influence the rotational speed of brushed motors, the brushes, the commutator, and other elements. Brush arcing can intensify the brush-to-commutator contact and can change at high speed. Most brushed motors also have a laminated iron core in their rotor, which increases their rotational inertia. It limits the electric bike motor's ability to accelerate and decelerate swiftly. Manufacturers can use strong magnets to make brushless motors, which are more expensive and have less rotational inertia.
Conclusion
In the field of electric propulsion, the brushless DC motor is a brilliant idea than a brushed motor that has revolutionized the field. Electric bikes and drones can function with optimum control and efficiency due to their straightforward and streamlined design.
Share:
Understanding the Need and Varieties of E-Bike Bags
Why Ebikes Have Different Weight Limits